Budowa maszyn roboczych
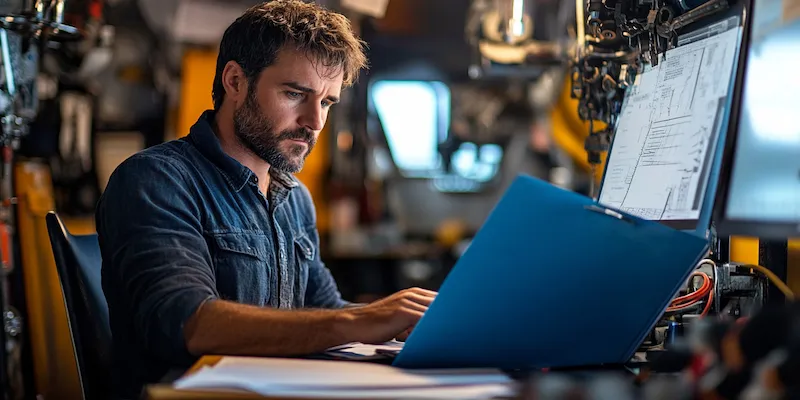
Budowa maszyn roboczych to złożony proces, który wymaga zrozumienia wielu podstawowych elementów. Każda maszyna robocza składa się z kilku kluczowych komponentów, które współpracują ze sobą, aby zapewnić efektywność i wydajność pracy. Do najważniejszych części należą silniki, które dostarczają energię do działania maszyny, oraz układy napędowe, które przekształcają tę energię w ruch. Kolejnym istotnym elementem są systemy hydrauliczne i pneumatyczne, które umożliwiają precyzyjne sterowanie ruchem oraz siłą roboczą. W przypadku maszyn roboczych często spotykamy się także z różnorodnymi narzędziami roboczymi, które są dostosowane do specyficznych zadań. Oprócz tego nie można zapomnieć o konstrukcji ramy, która musi być wystarczająco mocna, aby wytrzymać obciążenia podczas pracy. Właściwe połączenie tych wszystkich elementów jest kluczowe dla prawidłowego funkcjonowania maszyny i jej trwałości.
Jakie są najczęstsze zastosowania maszyn roboczych w przemyśle
Maszyny robocze odgrywają kluczową rolę w wielu sektorach przemysłu, a ich zastosowanie jest niezwykle różnorodne. W branży budowlanej wykorzystuje się je do wykonywania ciężkich prac, takich jak kopanie, transport materiałów czy podnoszenie ciężkich elementów. Przykłady to koparki, dźwigi oraz ładowarki. W przemyśle produkcyjnym maszyny robocze są niezbędne do automatyzacji procesów wytwórczych, co zwiększa wydajność i precyzję produkcji. W tym kontekście można wymienić roboty przemysłowe oraz maszyny CNC, które umożliwiają obróbkę metali i innych materiałów z dużą dokładnością. W rolnictwie maszyny takie jak ciągniki czy kombajny znacznie ułatwiają prace polowe i zbiorowe, co przyczynia się do zwiększenia plonów i efektywności gospodarstw rolnych. W logistyce natomiast wykorzystywane są wózki widłowe oraz systemy transportu wewnętrznego, które usprawniają procesy magazynowania i dystrybucji towarów.
Jakie innowacje technologiczne wpływają na budowę maszyn roboczych
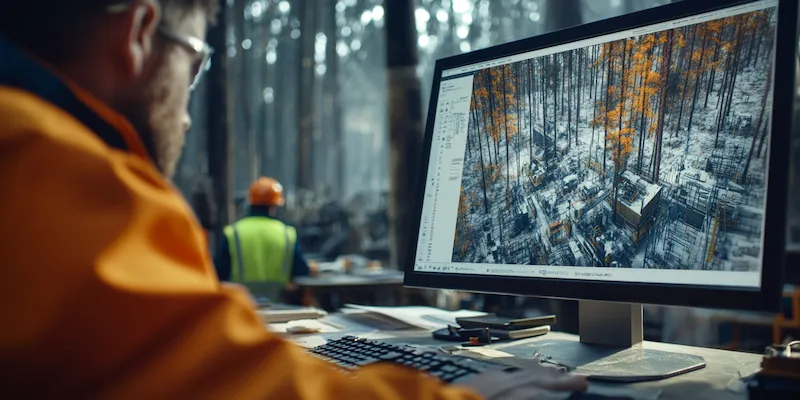
W ostatnich latach obserwujemy dynamiczny rozwój technologii, który ma znaczący wpływ na budowę maszyn roboczych. Innowacje te obejmują zarówno zaawansowane materiały, jak i nowoczesne systemy sterowania oraz automatyzacji. Wprowadzenie lekkich i wytrzymałych materiałów kompozytowych pozwala na zmniejszenie masy maszyn przy jednoczesnym zwiększeniu ich wytrzymałości. Dodatkowo technologie takie jak druk 3D umożliwiają szybkie prototypowanie oraz produkcję skomplikowanych komponentów w krótszym czasie i niższych kosztach. Automatyzacja procesów produkcyjnych dzięki zastosowaniu sztucznej inteligencji oraz robotyzacji przyczynia się do zwiększenia efektywności i precyzji działania maszyn roboczych. Systemy monitorowania w czasie rzeczywistym pozwalają na bieżąco śledzić stan techniczny maszyn oraz przewidywać awarie, co znacząco poprawia bezpieczeństwo pracy oraz zmniejsza koszty związane z naprawami. Również rozwój technologii IoT (Internet of Things) umożliwia integrację maszyn z siecią, co otwiera nowe możliwości w zakresie zarządzania flotą urządzeń oraz optymalizacji procesów produkcyjnych.
Jakie są kluczowe aspekty konserwacji maszyn roboczych
Konserwacja maszyn roboczych jest niezwykle istotnym aspektem ich użytkowania, który wpływa na efektywność pracy oraz bezpieczeństwo operatorów. Regularne przeglądy techniczne pozwalają na wczesne wykrywanie usterek oraz zapobieganie poważnym awariom, które mogą prowadzić do kosztownych przestojów w produkcji. Kluczowym elementem konserwacji jest smarowanie ruchomych części maszyny, co zmniejsza tarcie i zużycie podzespołów. Należy również regularnie sprawdzać stan układów hydraulicznych oraz pneumatycznych, aby zapewnić ich prawidłowe działanie. Warto zwrócić uwagę na czyszczenie filtrów powietrza i oleju, ponieważ ich zanieczyszczenie może prowadzić do spadku wydajności maszyny. Szkolenie operatorów w zakresie obsługi oraz konserwacji urządzeń jest równie ważne; dobrze przeszkolony personel potrafi szybko reagować na ewentualne problemy i dbać o sprzęt zgodnie z zaleceniami producenta.
Jakie są najważniejsze normy i przepisy dotyczące maszyn roboczych
Normy i przepisy dotyczące maszyn roboczych mają kluczowe znaczenie dla zapewnienia bezpieczeństwa ich użytkowania oraz ochrony środowiska. Wiele krajów wprowadza regulacje, które określają wymagania techniczne oraz procedury testowania maszyn przed ich wprowadzeniem na rynek. W Unii Europejskiej jednym z najważniejszych dokumentów jest Dyrektywa Maszynowa, która nakłada obowiązek spełnienia określonych norm bezpieczeństwa przez producentów. Normy te obejmują m.in. aspekty związane z konstrukcją, materiałami, a także systemami zabezpieczeń, które mają na celu minimalizowanie ryzyka wypadków podczas pracy z maszynami. Dodatkowo, wiele branż posiada swoje specyficzne regulacje, które uwzględniają szczególne warunki pracy oraz zagrożenia związane z danym sektorem. Przykładowo, w przemyśle budowlanym istnieją dodatkowe wymagania dotyczące maszyn używanych na placach budowy, takie jak konieczność posiadania odpowiednich certyfikatów oraz przeprowadzania regularnych inspekcji.
Jakie są różnice między maszynami roboczymi a urządzeniami przemysłowymi
Maszyny robocze i urządzenia przemysłowe to pojęcia często używane zamiennie, jednak istnieją istotne różnice między nimi. Maszyny robocze zazwyczaj odnoszą się do urządzeń zaprojektowanych do wykonywania konkretnych zadań w różnych branżach, takich jak budownictwo, rolnictwo czy produkcja. Przykładami mogą być koparki, ładowarki czy maszyny CNC. Z kolei urządzenia przemysłowe to szersza kategoria, która obejmuje nie tylko maszyny robocze, ale także inne sprzęty wykorzystywane w procesach produkcyjnych i technologicznych. Do urządzeń przemysłowych zaliczają się m.in. piece przemysłowe, kompresory czy systemy wentylacyjne. Różnice te dotyczą również funkcji i zastosowania; maszyny robocze są często bardziej wyspecjalizowane i skoncentrowane na konkretnych zadaniach, podczas gdy urządzenia przemysłowe mogą pełnić różnorodne funkcje w ramach szerszego procesu produkcyjnego.
Jakie są wyzwania związane z projektowaniem maszyn roboczych
Projektowanie maszyn roboczych wiąże się z wieloma wyzwaniami, które inżynierowie muszą uwzględnić na etapie tworzenia nowych rozwiązań technologicznych. Jednym z głównych wyzwań jest zapewnienie wysokiej wydajności przy jednoczesnym zachowaniu bezpieczeństwa użytkowników. Inżynierowie muszą znaleźć równowagę między mocą maszyny a jej stabilnością oraz odpornością na uszkodzenia mechaniczne. Kolejnym istotnym aspektem jest ergonomia; maszyny powinny być zaprojektowane tak, aby były łatwe w obsłudze i komfortowe dla operatorów. Wyzwania te stają się jeszcze bardziej skomplikowane w kontekście rosnących wymagań dotyczących ochrony środowiska oraz efektywności energetycznej. Projektanci muszą uwzględniać nowoczesne technologie i materiały, które pozwalają na zmniejszenie zużycia energii oraz emisji szkodliwych substancji. Dodatkowo zmieniające się przepisy prawne oraz normy bezpieczeństwa wymagają ciągłego dostosowywania projektów do aktualnych standardów rynkowych.
Jakie są trendy w rozwoju maszyn roboczych na przyszłość
Rozwój technologii wpływa na ewolucję maszyn roboczych i kształtuje ich przyszłość w wielu aspektach. Jednym z najważniejszych trendów jest automatyzacja procesów produkcyjnych oraz zwiększona integracja sztucznej inteligencji w działaniu maszyn. Dzięki tym technologiom możliwe jest osiągnięcie większej precyzji oraz efektywności operacyjnej, co przekłada się na niższe koszty produkcji i lepszą jakość produktów. Kolejnym istotnym trendem jest rozwój pojazdów autonomicznych, które mogą wykonywać zadania bez bezpośredniego nadzoru operatora. Takie rozwiązania znajdują zastosowanie zarówno w budownictwie, jak i w logistyce czy rolnictwie. W kontekście ochrony środowiska rośnie znaczenie zrównoważonego rozwoju; producenci coraz częściej poszukują sposobów na zmniejszenie zużycia energii oraz emisji CO2 przez maszyny robocze. Wykorzystanie odnawialnych źródeł energii oraz materiałów ekologicznych staje się standardem w projektowaniu nowych urządzeń. Ponadto rozwój Internetu rzeczy (IoT) umożliwia monitorowanie stanu technicznego maszyn w czasie rzeczywistym oraz optymalizację procesów produkcyjnych poprzez zbieranie danych analitycznych.
Jakie umiejętności są potrzebne do pracy z maszynami roboczymi
Praca z maszynami roboczymi wymaga od operatorów posiadania szeregu umiejętności technicznych oraz interpersonalnych. Kluczową kompetencją jest znajomość zasad działania konkretnej maszyny; operatorzy powinni być dobrze zaznajomieni z jej budową oraz funkcjonowaniem poszczególnych podzespołów. Umiejętność diagnozowania usterek oraz przeprowadzania podstawowych napraw jest równie ważna; szybka reakcja na problemy techniczne może znacznie zmniejszyć czas przestoju maszyny i związane z tym straty finansowe. Oprócz umiejętności technicznych istotne są także zdolności interpersonalne; operatorzy muszą umieć współpracować z innymi członkami zespołu oraz komunikować się efektywnie w sytuacjach kryzysowych. Znajomość zasad BHP jest niezbędna dla zapewnienia bezpieczeństwa podczas pracy z maszynami; operatorzy powinni być świadomi potencjalnych zagrożeń i umieć stosować odpowiednie procedury ochrony zdrowia i życia własnego oraz innych pracowników.