Destylator przemysłowy
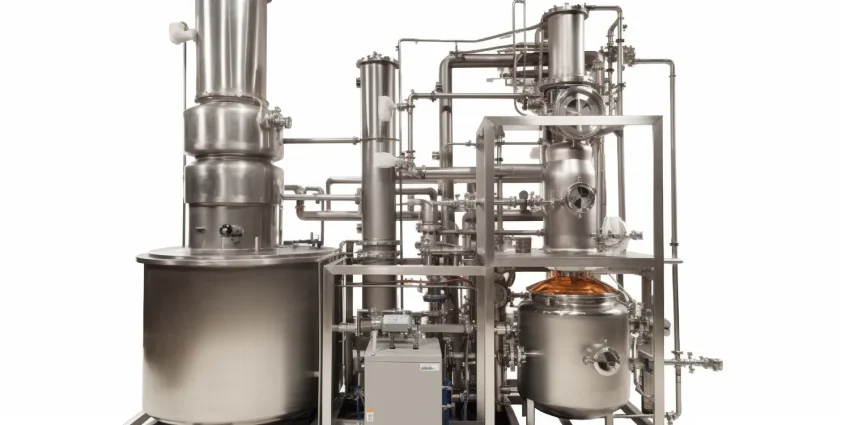
Destylator przemysłowy to zaawansowane urządzenie, które służy do separacji cieczy na podstawie różnicy ich temperatur wrzenia. Proces ten jest niezwykle istotny w wielu branżach, takich jak przemysł chemiczny, farmaceutyczny czy spożywczy. W destylacji wykorzystuje się zjawisko parowania, gdzie ciecz podgrzewana do określonej temperatury przekształca się w parę, a następnie schładza, aby skroplić się z powrotem do stanu ciekłego. W przypadku destylatorów przemysłowych, proces ten odbywa się w dużej skali, co wymaga zastosowania specjalistycznych technologii i materiałów odpornych na wysokie temperatury oraz ciśnienie. Warto również zauważyć, że destylatory przemysłowe mogą być wykorzystywane do produkcji różnych substancji, od alkoholu po chemikalia przemysłowe. Kluczowym elementem tego procesu jest kolumna destylacyjna, która pozwala na wielokrotne skraplanie i parowanie cieczy, co zwiększa efektywność separacji składników.
Jakie są rodzaje destylatorów przemysłowych dostępnych na rynku
Na rynku dostępnych jest wiele rodzajów destylatorów przemysłowych, które różnią się konstrukcją oraz przeznaczeniem. Najpopularniejsze z nich to destylatory prostolinijne, które charakteryzują się prostą budową i są stosunkowo łatwe w obsłudze. Kolejnym typem są destylatory frakcyjne, które umożliwiają oddzielanie składników o zbliżonych temperaturach wrzenia dzięki zastosowaniu kolumny frakcyjnej. Tego rodzaju urządzenia są szczególnie przydatne w przemyśle petrochemicznym oraz chemicznym, gdzie wymagana jest wysoka precyzja separacji. Istnieją także destylatory rotacyjne, które działają na zasadzie obrotu komory destylacyjnej, co zwiększa powierzchnię kontaktu między parą a cieczą. To rozwiązanie znajduje zastosowanie w laboratoriach oraz w produkcji małoskalowej. Warto również wspomnieć o destylatorach próżniowych, które działają w obniżonym ciśnieniu, co pozwala na destylację substancji w niższych temperaturach.
Jakie są zastosowania destylatorów przemysłowych w różnych branżach

Destylatory przemysłowe mają szerokie zastosowanie w różnych branżach, co czyni je niezwykle wszechstronnymi urządzeniami. W przemyśle chemicznym są one wykorzystywane do produkcji rozmaitych substancji chemicznych, takich jak kwasy czy alkohole. W branży farmaceutycznej proces destylacji jest kluczowy dla uzyskiwania czystych składników aktywnych stosowanych w lekach. Destylatory znajdują również zastosowanie w przemyśle spożywczym, zwłaszcza w produkcji napojów alkoholowych oraz olejków eterycznych. W przypadku alkoholi proces ten pozwala na uzyskanie wysokiej jakości trunków poprzez eliminację niepożądanych substancji. Ponadto destylatory są używane w przemyśle petrochemicznym do separacji różnych frakcji ropy naftowej, co jest niezbędne do produkcji paliw oraz innych produktów naftowych. Również w sektorze energetycznym destylacja odgrywa ważną rolę w procesach oczyszczania i recyklingu wody oraz innych cieczy.
Jakie są kluczowe elementy konstrukcyjne destylatora przemysłowego
Konstrukcja destylatora przemysłowego opiera się na kilku kluczowych elementach, które zapewniają jego prawidłowe działanie oraz efektywność procesu separacji. Podstawowym komponentem jest zbiornik do podgrzewania cieczy, który może być wyposażony w różnorodne źródła ciepła, takie jak palniki gazowe czy elektryczne grzałki. Kolejnym istotnym elementem jest kolumna destylacyjna, która umożliwia wielokrotne skraplanie i parowanie cieczy. Kolumna ta często zawiera różnego rodzaju packingi lub talerze, które zwiększają powierzchnię kontaktu między parą a cieczą. Ważnym aspektem konstrukcyjnym jest również system chłodzenia pary, który pozwala na skraplanie substancji i ich zbieranie w postaci cieczy. Dodatkowo nowoczesne destylatory mogą być wyposażone w automatyczne systemy kontroli temperatury oraz ciśnienia, co zwiększa bezpieczeństwo i efektywność procesu.
Jakie są koszty związane z zakupem destylatora przemysłowego
Koszty zakupu destylatora przemysłowego mogą się znacznie różnić w zależności od wielu czynników, takich jak typ urządzenia, jego wydajność oraz dodatkowe funkcje. Podstawowe modele destylatorów prostolinijnych mogą kosztować od kilku tysięcy do kilkunastu tysięcy złotych, co czyni je dostępnymi dla małych i średnich przedsiębiorstw. W przypadku bardziej zaawansowanych technologicznie destylatorów frakcyjnych lub rotacyjnych ceny mogą wzrosnąć do kilkudziesięciu tysięcy złotych, a nawet więcej, w zależności od specyfikacji. Dodatkowo, warto uwzględnić koszty eksploatacyjne, takie jak energia potrzebna do podgrzewania cieczy, konserwacja urządzenia oraz ewentualne naprawy. Warto również rozważyć koszty związane z instalacją oraz szkoleniem personelu, który będzie obsługiwał destylator. Inwestycja w wysokiej jakości destylator przemysłowy może przynieść znaczne oszczędności w dłuższej perspektywie, zwłaszcza jeśli chodzi o efektywność procesu produkcji oraz jakość uzyskiwanych produktów.
Jakie są najnowsze technologie w dziedzinie destylacji przemysłowej
W ostatnich latach nastąpił znaczny rozwój technologii związanych z destylacją przemysłową, co przyczyniło się do poprawy efektywności i jakości procesów produkcyjnych. Jednym z najnowszych trendów jest zastosowanie technologii membranowych, które pozwalają na separację składników bez konieczności podgrzewania cieczy. Tego rodzaju rozwiązania są szczególnie korzystne w przypadku substancji termolabilnych, które mogą ulegać degradacji pod wpływem wysokich temperatur. Innym innowacyjnym podejściem jest wykorzystanie systemów automatyzacji i monitorowania procesów, które umożliwiają zdalne zarządzanie destylatorami oraz optymalizację ich pracy. Dzięki zastosowaniu sztucznej inteligencji możliwe jest przewidywanie awarii oraz dostosowywanie parametrów pracy urządzenia do zmieniających się warunków. Ponadto coraz częściej stosuje się materiały kompozytowe i nanotechnologię w budowie elementów destylatorów, co zwiększa ich odporność na korozję i wydłuża żywotność.
Jakie są wyzwania związane z użytkowaniem destylatorów przemysłowych
Użytkowanie destylatorów przemysłowych wiąże się z szeregiem wyzwań, które mogą wpływać na efektywność procesów produkcyjnych oraz bezpieczeństwo pracy. Jednym z głównych problemów jest kontrola temperatury i ciśnienia w trakcie procesu destylacji. Niewłaściwe ustawienia mogą prowadzić do nieefektywnej separacji składników lub nawet uszkodzenia urządzenia. Dlatego tak ważne jest regularne monitorowanie tych parametrów oraz przeprowadzanie konserwacji sprzętu. Kolejnym wyzwaniem jest zarządzanie odpadami powstającymi podczas procesu destylacji. Wiele substancji chemicznych może być szkodliwych dla środowiska, dlatego konieczne jest wdrożenie odpowiednich procedur ich utylizacji lub recyklingu. Również szkolenie personelu obsługującego destylatory jest kluczowe; niewłaściwe użytkowanie urządzeń może prowadzić do poważnych awarii lub zagrożeń dla zdrowia pracowników. Dodatkowo zmieniające się przepisy prawne dotyczące ochrony środowiska oraz bezpieczeństwa pracy mogą wymuszać na przedsiębiorstwach dostosowywanie swoich procesów produkcyjnych do nowych norm.
Jakie są zalety korzystania z destylatora przemysłowego
Korzystanie z destylatora przemysłowego niesie ze sobą wiele korzyści, które mają kluczowe znaczenie dla efektywności procesów produkcyjnych w różnych branżach. Przede wszystkim umożliwia on uzyskanie wysokiej czystości produktów końcowych dzięki skutecznej separacji składników na podstawie różnicy temperatur wrzenia. To sprawia, że produkty otrzymywane za pomocą destylacji są często bardziej wartościowe i pożądane na rynku. Dodatkowo nowoczesne destylatory charakteryzują się dużą wydajnością, co pozwala na przetwarzanie dużych ilości surowców w krótkim czasie. Dzięki temu przedsiębiorstwa mogą zwiększyć swoją produkcję i obniżyć koszty jednostkowe. Kolejną zaletą jest możliwość automatyzacji procesów, co minimalizuje ryzyko błędów ludzkich oraz zwiększa bezpieczeństwo pracy. Warto również zauważyć, że wiele nowoczesnych destylatorów jest zaprojektowanych z myślą o minimalizacji zużycia energii oraz redukcji emisji szkodliwych substancji do atmosfery, co wpisuje się w globalne trendy proekologiczne.
Jakie są najczęstsze błędy przy obsłudze destylatora przemysłowego
Obsługa destylatora przemysłowego wymaga odpowiedniej wiedzy i doświadczenia, a błędy popełniane podczas tego procesu mogą prowadzić do poważnych konsekwencji zarówno dla jakości produktów, jak i bezpieczeństwa pracy. Jednym z najczęstszych błędów jest niewłaściwe ustawienie parametrów pracy urządzenia, takich jak temperatura czy ciśnienie. Niezgodność tych wartości z wymaganiami procesu może skutkować nieefektywną separacją składników lub uszkodzeniem sprzętu. Kolejnym problemem jest brak regularnej konserwacji urządzenia; zaniedbanie tego aspektu może prowadzić do awarii i kosztownych napraw. Często spotykanym błędem jest także niewłaściwe zarządzanie odpadami powstającymi podczas procesu destylacji; nieprzestrzeganie zasad utylizacji może prowadzić do naruszeń przepisów prawnych oraz szkód dla środowiska. Również niedostateczne szkolenie personelu obsługującego urządzenie może skutkować niebezpiecznymi sytuacjami w miejscu pracy.
Jakie są przyszłe kierunki rozwoju technologii destylacyjnej
Przemysłowa technologia destylacyjna znajduje się w ciągłym rozwoju, a przyszłość tej branży zapowiada się niezwykle obiecująco dzięki postępom technologicznym i rosnącym wymaganiom rynkowym. Jednym z kluczowych kierunków rozwoju jest dalsza automatyzacja procesów produkcyjnych; inteligentne systemy zarządzania będą coraz częściej integrowane z urządzeniami destylacyjnymi, co pozwoli na optymalizację ich działania oraz zwiększenie efektywności energetycznej. Ponadto rośnie zainteresowanie ekologicznymi metodami separacji składników; technologie takie jak ekstrakcja cieczy czy membranowa separacja stają się coraz bardziej popularne jako alternatywy dla tradycyjnej destylacji. W miarę jak przedsiębiorstwa stają przed wyzwaniami związanymi ze zmianami klimatycznymi i regulacjami dotyczącymi ochrony środowiska, poszukiwanie bardziej zrównoważonych metod produkcji stanie się priorytetem. Również rozwój materiałów odpornych na wysokie temperatury i korozję przyczyni się do zwiększenia trwałości i wydajności urządzeń destylacyjnych.